Lorsqu’une zone de travail est conditionnée (chauffage, refroidissement, contrôle de l’humidité, dépoussiérage, etc.), les consommations énergétiques liées à la ventilation de l’atelier sont de deux ordres :
- la consommation d’énergie électrique imputable aux ventilateurs qui va être directement liée aux débits et aux niveaux de perte de charge dans l’installation ;
- la consommation d’énergie thermique et électrique du conditionnement de l'air qui dépend fortement du débit d’air neuf admis.
La figure 1 qui présente la structure des dépenses énergétiques d'une installation de climatisation montre que le conditionnement peut représenter 70 % de la consommation du système contre 30 % pour la ventilation.
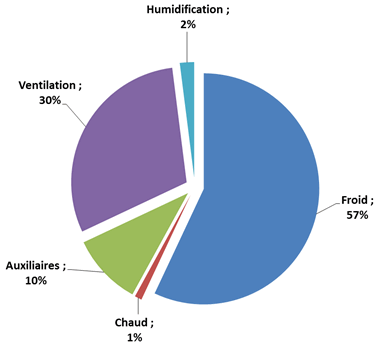
Figure 1 : Structure des dépenses énergétiques d'une installation de climatisation
En cas de conditionnement de l'air dans un atelier, une quantité d'énergie importante est généralement dépensée pour chauffer l'air, le refroidir, le sécher ou l'humidifier. Dans ce cas, pour optimiser sa consommation énergétique il sera primordial de réduire la quantité d'air à traiter (cf. exemple).
Règles de bonnes pratiques
- Réduire les quantités d'air à conditionner ;
- Préférer des systèmes de captage spécifique à des systèmes de ventilation générale ;
- Préférer une ventilation par déplacement à une ventilation par mélange ;
- Utiliser des récupérateurs d'énergie pour préchauffer l'air neuf avec l'air vicié ;
- Recycler l'air (Épuration obligatoire).
|
Exemple : Les gains énergétiques liés à la mise en place de systèmes de ventilation spécifique dans un atelier d’usinage
Les 2 scénarios proposés s’appliquent à un atelier d'usinage identique de 200 m2 (700 m3) dont le taux moyen d’occupation est de 10 personnes. Celui-ci contient huit tours d'usinage "petit diamètre" ainsi que deux tours d'usinage "grandes pièces".
Les consommations d’énergie ont été calculées sur la base des hypothèses suivantes :
- atelier chauffé et climatisé (humidité et température contrôlées) ;
- différence de température avec l’extérieur de 10°C.
Voici les résultats pouvant être attendus après la mise en place de systèmes de ventilation spécifique dans un atelier d’usinage à la place d'un système de ventilation générale.
Système |
Consommation relative (%) |
Description |
Ventilation générale
Débit de 3000 m3/h
|
100
|
Le brouillard d’huile généré par les différentes machines-outils n’est pas capté et se répand dans l'atelier. La ventilation générale est donc chargée de diluer la concentration du brouillard d’huile, ce qui nécessite un fort débit pour garantir une concentration inférieure aux concentrations recommandées. La consommation énergétique correspond à l’énergie nécessaire pour préchauffer les 3000 m3/h d’air neuf introduit par le réseau de ventilation, complétée par l’énergie électrique nécessaire pour un ventilateur de fort débit.
|
8 captages spécifiques sur petits tours d'usinage 2 captages spécifiques optimisés sur les grandes tours d'usinage Débit de 1000 m3/h 1 ventilation générale de 180 m3/h
|
80
|
Le brouillard est directement capté sur les machines avec une efficacité moyenne sur les petites machines mais élevée sur les machines de taille supérieure. Dans ce cas, le débit nécessaire à l’extraction des brouillards d’huile est très fortement réduit, ce qui entraine une réduction des 2 sources de consommation d'énergie. Le captage permet également de maîtriser beaucoup plus précisément les niveaux de concentration de polluants. On allie ainsi sécurité et réduction des coûts de fonctionnement
|
Les points forts :
- réduction de l'énergie nécessaire pour chauffer les locaux : le débit d'air à extraire est réduit ;
- sécurité améliorée : le captage des polluants est mieux maîtrisé.
|